Manufacturing Plant Relocation: A Comprehensive Guide
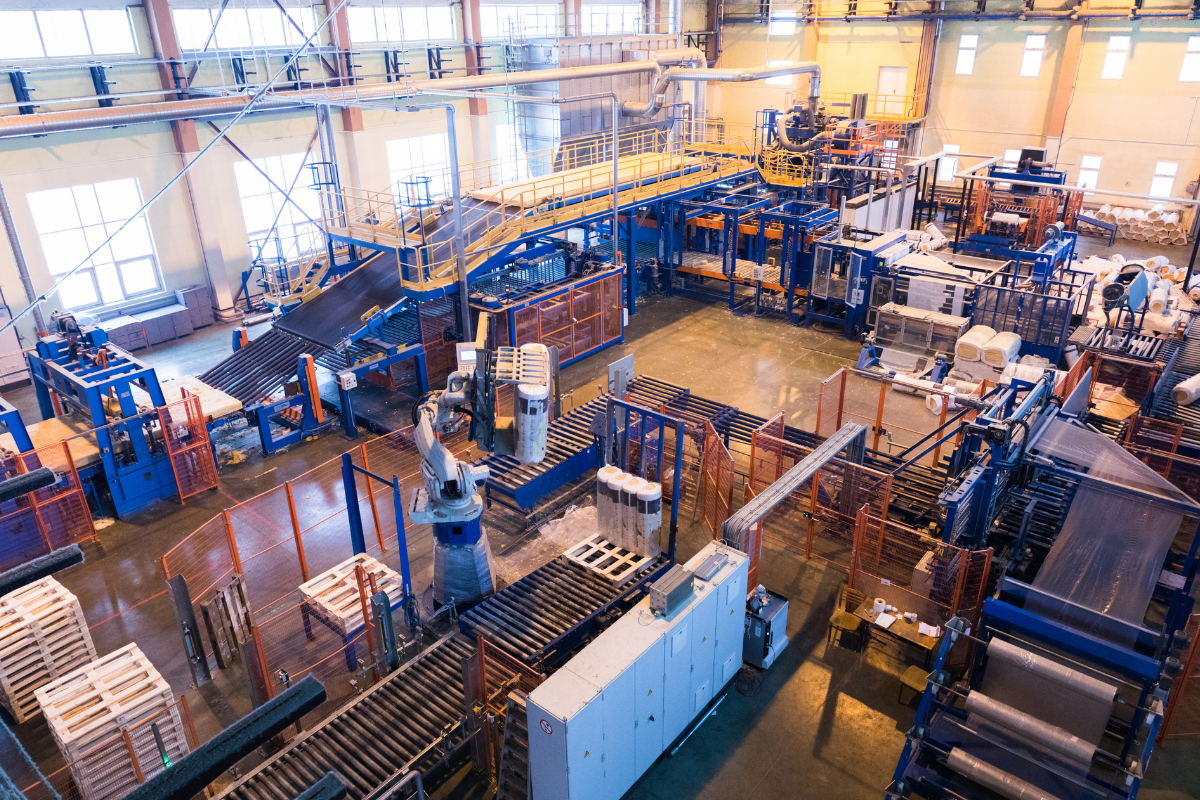
If your company has decided to move manufacturing operations to a new facility, undertaking a plant relocation requires thoughtful planning and coordination.
This complex process involves everything from machinery reinstallation to hiring and training new employees. By understanding key steps and establishing a detailed timeline, manufacturing teams can ensure operational continuity during this transition.
What to Know About Plant Relocation
Relocating production equipment and workflows presents unique challenges not inherent in other types of corporate moves. However, proper preparation and support can streamline plant transfers and minimize downtime. This guide covers equipment audits, staggered timelines, facility evaluation criteria, employee onboarding, community relations, and other relocation essentials for manufacturing firms.
Auditing Existing Assets and Layouts
Before boxing up tools, account for all physical assets and machinery needing transfer. Compile detailed lists noting specifications, power sources, connections, computer integrations, and other infrastructure ties.
Use these audits to assess compatibility with the future plant’s layout and begin developing potential installation timelines for seamless operations resumption.
Another early step? Survey current factory floor plans and workflows. Evaluate material routing efficiencies, production output, quality control measures, and inventory areas.
Assess what works well versus processes needing improvement. This analysis should inform equipment arrangements and facility relocation project plans within the new space.
Developing a Phased Relocation Timeline
When relocating manufacturing equipment, avoid shutting down all operations during the move. With thoughtful staging, teams can shift individual assembly lines before resuming output in the new facility.
For example, transfer packaging functions first before relocating primary production machinery during a secondary stage.
During each phase, allocate extra staff to fine-tune new equipment installations and workflows through training runs.
Confirm all quality benchmarks and output quotas are achievable before beginning the following relocation sequence. With incremental transitions, companies maintain revenue streams while reallocating resources.
Choosing a Facility Meeting Operational Goals
What features make an ideal plant for reaching growth and innovation goals? When assessing relocation options, consider must-haves like:
- Expansive Production Space: Accommodate current and future machinery needs, inventory staging, shipping docks, and efficient layouts. Factors in all specialized requirements include ventilation, material hoists, or reinforced flooring.
- Technology Infrastructure: Ensure modern electrical, internet, computer networks, and automation systems for supporting operations. Evaluate backup power sources as well.
- Access Considerations: Keep travel convenient for essential employee transit, vendor deliveries, customer visits, and product distribution channels.
- Compliance Assurances: Verify all structural, safety, zoning, environmental, and local compliance codes are met through inspections.
- Growth Flexibility: Even if current space needs are met, ensure the location offers room for expanding manufacturing lines as product demands increase.
While turnkey building customization may appeal to faster occupancy, reusing older facilities can achieve comparable results through renovations aligned with equipment needs.
Leveraging Experienced Plant Relocation Partners
While keeping factory relocations in-house may seem more budget-friendly, the complexity involved makes working with an experienced materials handling and rigging provider well worth the investment. Look for partners offering full-service support spanning:
- Project Management & Consultation: Supplement internal teams by designating an account representative to quarterback end-to-end coordination. Choose providers with expertise tailored to manufacturing for input on equipment specifications, layout efficiencies, recommended timelines, and insights addressing regulatory considerations.
- Equipment Preparation: Depend on turnkey crating and preparations tailored to fragile machinery components requiring delicate handling. Experts also assist with proper machine disconnections and deinstallations based on dimensions and infrastructure needs.
- Logistics Management: Leave equipment packing, loading, and trucking logistics to specialists equipped for oversized deliveries and installations. They’ll also track assets in transit while managing claims, or exception issues should any arise.
- Storage & Security: If equipment transfers must be staged pending build outs, utilize partners with secure warehouses designed explicitly for machinery and sensitive inventory storage between locations.
- Installation Services: Have resources ready upon delivery for immediate reinstallations, wiring reconnections, and trial machinery runs to confirm proper functionality in new onsite locations. Identify any post-move troubleshooting needs before resuming all operations.
By outsourcing the heavy lifting of transporting tons of equipment, internal teams can focus on operational transitions, new hire onboarding, inventory controls, and maintaining customer shipments through move periods.
Let experts fluent in equipment intricacies handle intensive coordination. The upfront investment pays dividends through faster relocation completions and minimized downtime or cost overruns.
Relocating Staff or Hiring Local Talent
Manufacturing relocations significantly impact personnel who oversee equipment operations, quality testing, supply chain coordination, inventory control, and product distribution. Assess whether you want to practice internal mobility, or hire new staff native to the region.
Relocating trusted talent retains accumulated expertise, while new hires necessitate extensive training. Evaluate salary and benefits packages to keep tenured staff while staying attractive to fresh regional recruits. Be sensitive too in transition conversations – a move may not suit some employees’ families or lifestyles.
Also, weigh local tax incentives for creating new jobs against relocation packages offered to transfer staff. Take staffing culture fit into account as well. Integrating legacy and recent hires, post-move may influence onboarding timelines and impact output as teams mesh.
Getting Community Buy-In
How manufacturing facilities affect surrounding neighborhoods influences local support for a plant relocation. Prioritize community outreach from the project’s outset. Be transparent about operational impacts in areas like:
- Traffic: Will increased truck activity or employee commuting disrupt neighborhoods? Discuss mitigation options.
- Environment: Address how new machinery or production changes could alter emissions, waste disposal needs, utility usage, or drainage.
- Aesthetics: Consider visual buffers like fencing or landscaping to blend industrial architecture into communal spaces.
- Safety: Spotlight security upgrades and emergency protocols to minimize risks of industrial accidents affecting residents.
Also, discuss economic benefits. Tout job creation, local vendor relationships, hospitality purchases from employee meals and travel, and tax contributions. Back messages with action, too – will the company fund community growth grants or civic initiatives? Making constituents partners in relocation success builds goodwill.
Key Relocation Preparations Recap
While every plant transfer carries unique considerations, follow these general steps for smooth execution:
- Conduct equipment, inventory, and workflow audits pre-move to facilitate appropriate installations in the new facility.
- Develop phased timelines for shifting operations incrementally before the current lease expires.
- Choose a new facility accommodating current and future production capacity with infrastructure to match equipment needs.
- Determine the best options for relocating or hiring staff required for the new plant location.
- Earn community buy-in by addressing local impact concerns transparently while spotlighting economic benefits.
With detailed checklists guiding all relocation preparation facets, manufacturing transitions can minimize financial risks and operational disruptions. While complex, plant relocations with thoughtful direction enable reaching production potential in optimal new environments.
Relocation Checklists Keep Complex Moves Organized
To keep myriad details moving apace across months-long manufacturing plant relocation timelines, create master checklists assigning ownership for crucial milestones. Separate lists by functional area like:
Equipment Relocation
- Audit machinery, tools, and assets (Specialist Lead)
- Map current/future layout options (Operations Lead)
- Identify rigging/transport needs with timeline (Logistics Lead)
- Schedule incremental equipment shutdown/move/install dates (Operations Lead)
- Confirm IT systems, power, and safety preparedness (Facility Lead)
Inventory Controls & Supply Chain
- Audit raw material stocks (Inventory Lead)
- Schedule staggered inventory freezes/transfers/receiving (Inventory Lead)
- Validate supplier deliveries/contracts align to new site (Supply Chain Lead)
- Secure storage spacing & material handling equipment (Facility Lead)
Staffing/Training Transitions
- Assess current staff relocation interests (HR Lead)
- Develop local hiring plan with rollout timing (HR Lead)
- Vet regional recruiting and staffing partners (HR Lead)
- Design training for new hires/incumbent staff on equipment/workflows (Operations Lead)
The lists above highlight operations, logistics, facilities, inventory, supply chain, IT, and HR responsibilities. Update statuses regularly. Schedule oversight meetings to identify any resource gaps or roadblocks needing executive input.
Relocating an entire manufacturing plant takes military-level precision. Following formal plans while regularly syncing with all personnel in charge of critical pieces sets the stage for success. With coordinated checklists guiding activities, companies can meet aggressive timelines while minimizing disruption.
Plant Relocation: FAQs
How early should we start planning for a manufacturing relocation?
Ideally, 12-18 months out. Audits, construction bids, equipment disassembly/rewiring, and hiring/training require significant lead time. Building in contingencies is wise, too, given potential delays in finalizing new leases or permits.
What costs most surprise companies mid-relocation?
Hidden IT, inventory transfer, specialized equipment rigging, and employee retraining/relocation expenses often exceed initial budget estimates. Pad estimates by 20% to cover unexpected overages. Also confirm what (if any) legacy facility exit penalties apply depending on lease termination clauses too.
Is directly transferring current equipment smart?
While convenient, newer machinery may improve efficiency, safety, or output. Evaluate upgrading certain lines balanced against the available capital budget rather than defaulting to legacy equipment.
Should we use a relocation project manager?
Experienced project managers adept at complex plant transfers provide valuable oversight given the multifaceted coordination involved. Well worth the investment. They alleviate internal team bandwidth challenges through crunch times.
What operational snags commonly arise post-move?
Rewiring machines in new layouts causes functionality glitches as teams adjust. Expect short-term dips reestablishing quality controls and output rhythms as staff settles into new spaces. Plan for 3-6 month optimization periods.
Final Thoughts
Smooth manufacturing relocations require strategic planning, phased equipment transfers, facility infrastructures supporting operations, attentive personnel transitions, and community goodwill.
While intricate, businesses that leverage relocation experts and follow detailed checklists can thrive post-move by reaching production goals in optimal new plant locations. With crucial best practices in place, companies can ultimately minimize disruption while accelerating future growth.
If you are considering a plant relocation for your company, ARC Relocation can help make your transition easy. Contact ARC Relocation today to set up a free consultation call.