The Ultimate Guide to Pharmaceutical Plant Relocation
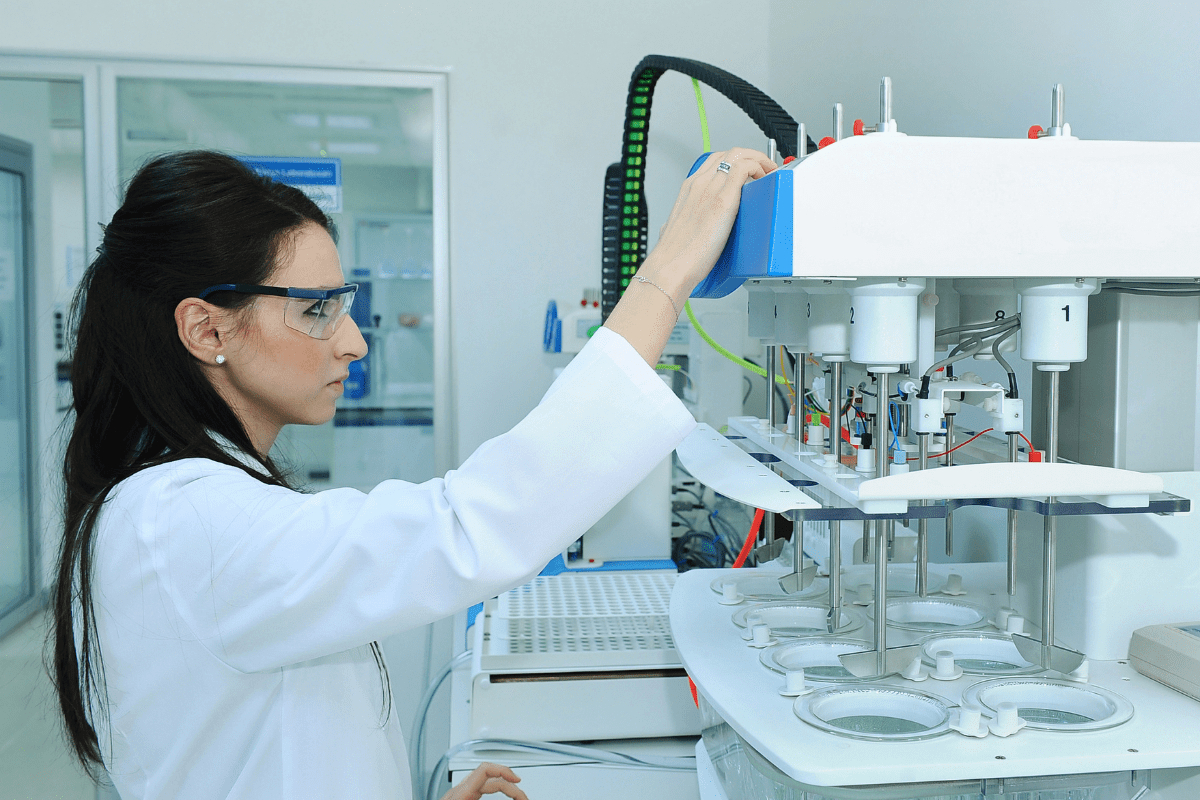
A pharmaceutical plant relocation is not a simple task. It’s a difficult operation that requires meticulous planning, coordination, and execution.
From regulatory compliance to validation, there are a ton of factors to consider to ensure a smooth transition while minimizing down time and maintaining product quality.
What to Know About Pharmaceutical Plant Relocation
There are a few unique challenges when it comes to a pharmaceutical plant relocation that aren’t found in typical plant relocations. There are stringent regulatory requirements, strict quality control measures, and there’s a need to maintain product integrity throughout the relocation process.
Auditing Existing Assets and Processes
Before starting your pharmaceutical plant relocation, it’s important to conduct a thorough audit of all existing assets, equipment, and processes. This includes documenting specifications, power requirements, computer integrations, and any specialized infrastructure needs.
Additionally, evaluate current workflows, material handling procedures, and quality control measures to identify areas for improvement in the new facility.
Ensuring Regulatory Compliance
The pharmaceutical industry is heavily regulated, and maintaining compliance is so important during a plant relocation. Be sure to engage with regulatory authorities early in the process to understand and comply with all relevant guidelines and regulations.
This could involve obtaining necessary approvals, licenses, and certifications for the new facility, as well as ensuring that equipment validation and qualification procedures are followed meticulously.
Developing a Phased Relocation Timeline
To help minimize disruptions and maintain product supply, a phased relocation approach is often recommended. This involves transferring operations in stages, such as moving packaging lines first, followed by primary production machinery.
During each phase, allocate adequate time and resources for equipment installation, qualification, and validation, as well as staff training on new processes and workflows.
Choosing a Facility Tailored for Pharmaceutical Manufacturing
When selecting a new facility, consider factors that are critical for pharmaceutical operations. These include:
- Specialized infrastructure requirements (for example: cleanrooms, controlled environments, utilities, and backup systems)
- Adequate space for production, storage, and quality control laboratories
- Compliance with current Good Manufacturing Practices (GMP) and other regulatory standards
- Flexibility for future expansion and growth
Partnering with Experienced Relocation Specialists
Given how complex and important it is to maintain product quality and compliance, it’s highly recommended to partner with experienced relocation specialists who have expertise in the pharmaceutical industry, like ARC Relocation.
These specialists can provide valuable guidance and support throughout the entire process, including project management, equipment preparation, logistics, storage, and installation services.
Transitioning and Training Personnel
A successful plant relocation heavily relies on the expertise and competence of your workforce. Assess whether you will practice internal mobility or hire new personnel local to the new facility.
Be sure to go over your relocation packages with your employees so they can decide whether they want to stay on board with your company before the relocation. If not, you will need to hire new personnel.
In either case, training programs should be implemented to ensure a seamless integration into the new environment and adherence to updated processes and procedures.
Community Relations and Environmental Considerations
Pharmaceutical manufacturing operations can have significant impacts on the surrounding community and environment. You should proactively address concerns related to traffic, emissions, waste disposal, and safety protocols.
Additionally, highlight the economic benefits and potential community initiatives that the new facility will bring to the area.
Inventory Control and Supply Chain
Before initiating the relocation process, conduct an audit of all raw materials, work-in-progress, and finished goods inventory. This will help you understand the volume of materials that need to be transferred and plan accordingly.
Develop a detailed inventory management plan that outlines the steps for freezing, transferring, and receiving inventory at the new facility.
Pharmaceutical inventory often requires specific storage conditions, such as temperature and humidity control. Ensure that the new facility has adequate storage spaces that meet these requirements.
You should invest in appropriate material handling equipment, such as forklifts, pallet jacks, and specialized carts, to safely and efficiently move inventory during the relocation process.
Communicate early and often with your suppliers to ensure a seamless transition of raw material deliveries to the new facility. Review and update supplier contracts, shipping addresses, and delivery schedules to reflect the new location.
Consider implementing contingency plans, such as maintaining safety stock levels or identifying alternative suppliers, to mitigate potential supply chain disruptions during the relocation period.
Key Relocation Preparations Recap
To ensure a smooth pharmaceutical plant relocation, follow these key steps:
- Conduct thorough audits of existing assets, processes, and workflows
- Ensure compliance with regulatory requirements and obtain necessary approvals
- Develop a phased relocation timeline to minimize disruptions
- Choose a facility tailored to pharmaceutical manufacturing needs
- Partner with experienced relocation specialists
- Implement comprehensive personnel training programs
- Address community and environmental concerns proactively
- Manage your inventory and supply chain
Pharmaceutical Plant Relocation: FAQs
How far in advance should we start planning for a pharmaceutical plant relocation?
It’s recommended to start the planning process at least 12-18 months in advance. The lengthy timelines are necessary to accommodate regulatory approvals, equipment validation, personnel training, and other critical aspects of the relocation.
What are the most significant regulatory challenges faced during a pharmaceutical plant relocation?
Maintaining compliance with Good Manufacturing Practices (GMP), obtaining necessary licenses and certifications for the new facility, and ensuring proper equipment validation and qualification procedures are followed are among the most significant regulatory challenges.
Should we consider relocating existing equipment or investing in new equipment?
While relocating existing equipment may seem more cost-effective initially, it’s crucial to evaluate the long-term benefits of investing in new, state-of-the-art equipment.
Newer equipment can often improve efficiency, product quality, and compliance with evolving regulatory standards.
How can we minimize disruptions to product supply during the relocation?
Implementing a phased relocation approach, where operations are transferred in stages, can help minimize disruptions to product supply.
Additionally, maintaining open communication with customers and suppliers, and strategically managing inventory levels can mitigate potential supply chain issues.
What role do relocation specialists play in a pharmaceutical plant relocation?
Experienced relocation specialists with expertise in the pharmaceutical industry can provide invaluable support throughout the entire process.
They can assist with project management, equipment preparation, logistics, storage, installation services, and ensuring compliance with regulatory requirements.
Final Thoughts
A pharmaceutical plant relocation is not only challenging, but it is complex. With proper planning, execution, and the right expertise, it can be accomplished successfully.
By following the guidelines outlined in this guide, pharmaceutical companies can navigate the delicate and difficult process while maintaining product quality, regulatory compliance, and operational continuity.
ARC Relocation can help with your company’s plant relocation. Contact ARC Relocation today to set up a free consultation call.