Warehouse Moving: What to Know When Planning Your Warehouse Move
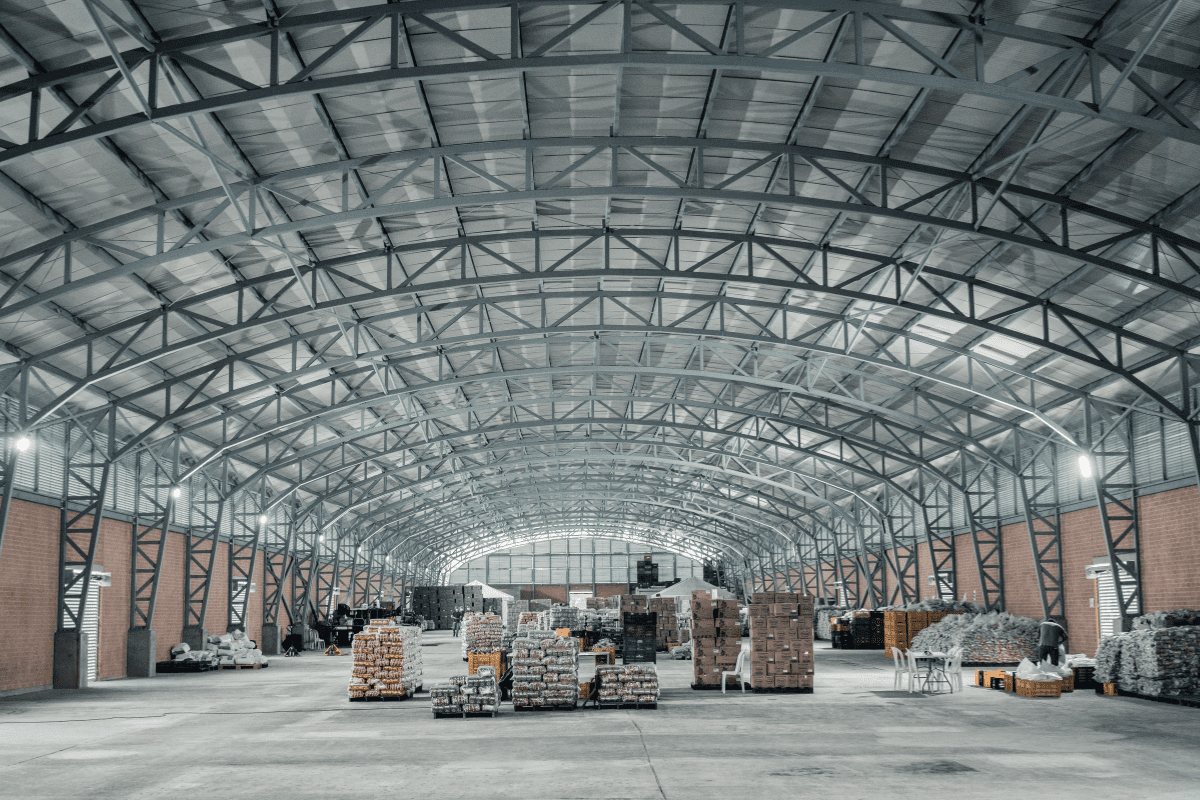
Moving a warehouse is no small task. With inventory, equipment, and operations to manage, careful planning is essential for a smooth transition to your new facility.
Understanding timing, budgets, logistics, and staffing needs well in advance will help your relocation go as seamlessly as possible.
What to Know About Warehouse Moving
Relocating a warehouse is an immense undertaking requiring extensive planning across many functional areas. Solutions must be coordinated internally and with specialized external teams, from assessing future business needs to equipment logistics to final cleaning transitions.
While highly disruptive to daily operations, a warehouse move also presents opportunities. Upgraded spaces can improve workflows, inventory systems, technology infrastructure, and environmental controls – all leveraged to lift production output and employee experiences for years.
Approaching this project with ample preparation timelines, clear communications plans, and firm budget guidance allows businesses to minimize revenue losses during transitions. Using business relocation services and partnering with professional commercial movers further alleviates planning burdens on internal staff.
Meticulous oversight of logistics details, verified inventory tracking, timed equipment rebuilding, and strict staging plans enable seamless warehouse changeovers even at massive scales. Maintain construction and moving checklists to keep projects on task, on time, and optimized for operational excellence.
When relocating your business, understanding these factors can ensure the move runs as planned.
Selecting a New Space
It all starts with finding a suitable new warehouse space for your business. Consider size, layout, proximity to transportation routes, office spaces, and more when touring candidate buildings or leased spaces:
- Ensure adequate square footage, ceiling clearance height, loading docks, and parking availability for staff and commercial vehicles—factor in current needs and potential growth
- Look for modern electrical, lighting, shelving, and climate-controlled options for inventory and operations
- Confirm the space meets all safety codes and qualifications for warehousing standards
Are you relocating employees? Will these employees need to purchase a new home in their new location? Are they selling an existing home? If so, the ARC Realtor Rebate can help them save thousands of dollars in real estate commissions. We’ve worked with hundreds of people in your situation and would be happy to help. Click below to learn more.
Creating a Detailed Moving Plan
Just like you would need to create an office relocation checklist, you also need to plan a checklist for moving your warehouse. With a new location secured, you can map out a detailed plan for moving day:
Communication Planning
- Inform staff, suppliers, transport companies, and clients of relocation timelines and contingencies well ahead of time
- Provide new address details and points of contact for deliveries or shipments in transit during the move
- Establish procedures for accessing inventory or records
Inventory Management
Precise inventory tracking minimizes losses and confusion when shifting stock to the new warehouse:
- Categorize and label inventory for easy identification. Conduct counts before and after the move
- Organize items onto pallets or in crates based on priority and destination within new warehouse layouts
Equipment Logistics
- Identify needs for properly disconnecting, transporting, and setting up equipment
- Determine if machines require recalibration or inspection after reinstallation
- Arrange for rental of forklifts, pallet jacks, or other equipment as needed
Delegate warehouse move responsibilities across staff based on roles:
- Assign managers to oversee zones or tasks, with laborers assisting.
- Hire temporary workers or coordinate staff volunteers to supplement if needed.
Establishing a Moving Budget
- Calculate costs for inventory transport, equipment disassembly/reinstallation, and staff hours
- Factor in expenses of new lease, parking lots, office furnishings, cabling, and more
- Account for revenue losses from warehouse downtime during the transition
Addressing Safety and Compliance
- Confirm that the new warehouse meets all fire safety, zoning, ADA, and other regulatory standards
- Update insurance policies, licenses, and legal business registrations for change of occupancy
Cleaning and Facility Transitions
- Schedule deep cleaning, rubbish removal, and parking space designation at both old and new sites
- Coordinate timing for final inventory load-out, inspection walkthroughs, and key handoffs
Managing Inventory and Stock Levels
- Plan to scale down inventory receipt shipments 4-6 weeks before the move
- Establish backup storage contingencies and timelines for access if needed
- Structure inventory load-out by priority: high turnover & value items first
Handling Warehouse Machinery & Equipment Relocation
Effectively transporting machinery and handling the disconnection and reinstallation of warehouse equipment requires precision and expertise. You can swiftly resume operations at your new facility by correctly coordinating these moves.
Inventory Warehouse Equipment & Connections
Compile a list of all warehouse equipment and corresponding utility connections that will need to be moved:
- Incorporate the power requirements of machines along with connectivity types, such as 3-phase, water, HVAC, or nitrogen
- Catalog exact technical specifications and measurements for dismantling and reassembly
- Capture pictures of all equipment layouts and cabling connections for each
Schedule Specialized Movers & Contractors
While warehouse staff can handle packing and standard moving, coordinate with specialists for machinery and systems:
- Reserve qualified machine riggers and movers for equipment dismantling, hoisting, transport, and rebuilds
- Arrange electrical, plumbing, and low-voltage contractors to re-establish connections
- Consider hiring project managers for oversight of timelines, inspections, and licenses
Map Temporary Power & Storage Contingencies
Minimize downtime by arranging backup power sources or equipment storage with movers if needed:
- Plan for temporary generators to power priority equipment during transition periods
- Explore options for short-term machinery storage facilities if rebuilds will exceed a few days
- Rent portable backup cooling or freezer units to protect sensitive stock or materials
Maintain Equipment Calibration & Certifications
Prevent the loss of calibrated machinery accuracy and production output after moves:
- Schedule manufacturers to recertify critical equipment like scales or heat processors
- Identify needs for load testing, vapor recovery testing, and pressure certifications after installations
- Include expenses for manufacturers to re-calibrate machinery sensors, blades, or robots post-move
Prioritize & Stagger Strategic Equipment Relocation
Carefully structure equipment dismantling & rebuilding to support ongoing warehouse functions:
- Disable lower priority or redundant systems first while keeping mission-critical units operating
- Plan multi-phase timelines for relocating groups of machines based on processes and dependencies
- Allow 2+ weeks for specialists to rebuild and inspect reconnected equipment methodically
Employ strategic planning, experienced crews, and faithful machine moving checklists to streamline transitions of even the most complex warehouse machinery installations across facilities. Maintain operational capacities from old to new spaces for optimized results.
Key Warehouse Relocation Recap
Orchestrating a seamless warehouse transition plan takes advanced preparation, strict attention to detail, and careful logistical coordination. Be sure to:
- Tour candidate spaces 6-12 months before lease expiration
- Create detailed floor plans of current and new layouts
- Set a schedule with milestones for planning, packing, and moving
- Arrange logistics for security, utilities, technology, and administrative needs
- Establish cleaning and repair checklists for vacate and move-in
- Brief staff regularly as plans progress
Careful oversight of logistics details, contingency preparation, and timely coordination of external crews and staff will ensure your warehouse relocation proceeds efficiently.
Warehouse Moving Checklist
Use this comprehensive checklist when coordinating your warehouse move, beginning 6-12 months in advance:
6-12 Months Prior
- Explore potential buildings or spaces for relocation needs
- Project growth requirements for size, layout, and technology
- Develop a proposal for ownership on an ideal relocation timeline and budget
4-8 Months Out
- Finalize new warehouse lease agreement
- Create layout blueprints and begin design modifications if needed
- Plan logistics for inventory audits, transport, staffing
- Update business databases with new address
2-4 Months To Go
- Categorize current inventory and equipment for the move
- Photograph existing layouts and label shelves, equipment locations
- Assign staff move coordinators and temporary laborers as needed
- Reserve moving vehicles, equipment rentals, and suppliers
4-6 Weeks Out
- Confirm new space construction or modifications complete, if needed
- Schedule cleaning, rubbish removal, and parking logistics
- Start inventory pack up and documentation per move plan
2 Weeks Prior
- Finalize moving vehicle schedules and equipment rentals
- Complete notifications to clients, vendors, and key contacts
- Conduct preparatory staff relocation training or briefings
- Begin technology and administrative office relocation
Moving Days
- Oversee inventory and equipment load-outs per plan
- Document load-out and intake processes
- Verify utility connections and technology reactivations
- Complete final cleaning and rubbish removal walkthroughs
Warehouse Moving: FAQs
How early should we start planning the warehouse move?
Ideally, it should be 12 months from a lease renewal or desired relocation timeline. This allows ample time for space exploration, budgeting, inventory planning, and staff coordination.
What costs should we budget for the warehouse move?
Major expenses may include new lease deposits and fees, inventory transport vehicles, temporary storage, equipment disassembly or reinstallation, utility connections, cleaning services, and potential overtime pay for staff. Also, factor in business losses from any downtime during the transition.
How do we prevent inventory losses during a warehouse move?
Meticulously categorize and document all inventory before packing onto pallets or crates, keeping high-value items secure. Conduct thorough counts before warehouse exit, upon truck loading, and again on intake to the new warehouse. Establish procedures for reconciling any inventory discrepancies.
What staffing considerations are needed for warehouse relocations?
Determine if additional temporary laborers are required to assist with packing and heavy lifting work. Confirm the availability of drivers and equipment operators such as forklift workers. Also, assign coordinators and managers for oversight. Evaluate hourly or contractor rates to allocate budget.
Final Thoughts
While entailing extensive coordination, an adequately planned warehouse relocation positions your business for continued success and growth at a new, upgraded location.
Your investment of time into strategic space selection, thorough pre-planning, and smooth operational transitions ultimately pays dividends through lifting staff productivity and customer service for years to come.
Partner with professional commercial movers and take advantage of available warehouse moving checklists to keep your next relocation on time, on budget, and optimized for the future.
If you are considering a warehouse relocation for your company, ARC Relocation can help. Contact ARC Relocation today to set up a free consultation call.